Injection Mold Manufacturer: Quality and Precision in Metal Fabrication
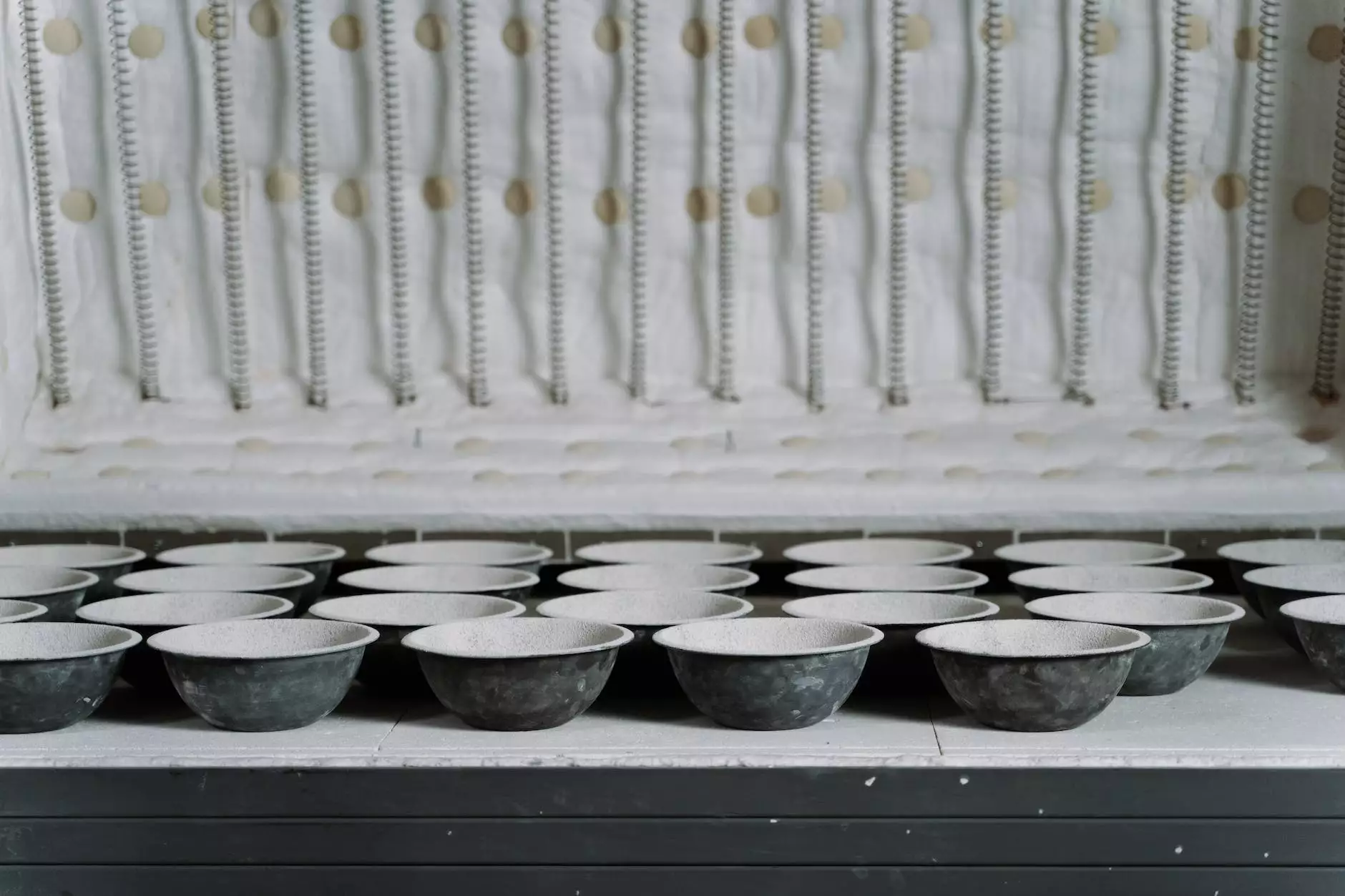
In today's fast-paced manufacturing environment, the role of an injection mold manufacturer is pivotal in the production of intricate components and applications across industries. The demand for high-quality, precision-engineered products has never been higher, validating the integral position that these manufacturers occupy. In this comprehensive guide, we will delve deep into the processes, benefits, and future of injection molding within the context of the metal fabrication sector.
The Essence of Injection Molding
Injection molding is a manufacturing process for producing parts by injecting molten material into a mold. It is primarily used for metal and plastic but varies widely depending on the type of material being molded. The process is characterized by its efficiency, repeatability, and the ability to produce complex shapes that might be impractical with traditional methods.
How Injection Molding Works
The injection molding process generally involves the following steps:
- Material Preparation: Materials, typically in the form of granules, are fed into a heated barrel.
- Melting: The material is heated until it becomes molten.
- Injection: The molten material is injected into a mold at high pressure.
- Cooling: The material cools and solidifies within the mold.
- Ejection: The finished part is ejected from the mold.
Each of these steps is crucial in ensuring that the final product maintains the desired strength, detail, and surface finish.
Benefits of Choosing a Professional Injection Mold Manufacturer
Selecting the right injection mold manufacturer can directly impact the quality of the products, operational efficiency, and overall costs. Here are some compelling benefits:
1. Superior Precision and Quality Control
With advanced technology and skilled experts, a professional manufacturer ensures that every injection molded part meets stringent quality standards. This quality control is achieved through:
- State-of-the-art Equipment: Utilizing the latest manufacturing technology increases production accuracy.
- Consistent Processes: Established workflows minimize variability and defects.
- Expert Oversight: Experienced engineers oversee production, ensuring adherence to quality metrics.
2. Cost-Efficiency in Production
Initially, the setup costs for injection molding can be significant; however, over time, these costs are offset by the ability to produce high volumes at lower per-unit costs. Additional cost-saving benefits include:
- Reduced Material Waste: The precision of the process leads to less waste material.
- Faster Prototyping: Quick iterations on designs can significantly reduce development costs.
- Scalability: High-speed production runs can be implemented as demand increases.
3. Versatility Across Industries
The versatility of injection molding makes it applicable to various industries, including:
- Automotive: Creating complex parts like dashboards, housings, and more.
- Electronics: Manufacturing components with intricate details for electronic devices.
- Medical Devices: Producing precise parts that meet regulatory standards.
- Consumer Goods: Designing a range of everyday products from bottles to household items.
Injection Mold Manufacturer: The Innovators of Today
Adapting to the ever-changing market demands requires innovation. The modern injection mold manufacturer embraces new technologies and methods to remain competitive. Key innovations include:
1. Advanced Materials
The development of new and improved materials enhances the capabilities of injection molding. This includes:
- High-strength plastics to reduce weight in automotive parts.
- Bio-based materials for environmentally friendly products.
- Composite materials that combine the best properties of various substances.
2. Automation and Robotics
Automation has transformed injection molding, introducing:
- Robotic arms for precise material placement and handling.
- Automated quality inspection systems using AI technologies.
- Predictive maintenance systems that minimize downtime.
3. Industry 4.0 Integration
The rise of Industry 4.0 means incorporating smart manufacturing practices, such as:
- Data analytics to optimize processes and reduce waste.
- Cloud computing for improved supply chain management, allowing better resource planning and forecasting.
- IoT devices for real-time monitoring and control of the manufacturing process.
DeepMould: Your Trusted Injection Mold Manufacturer
At DeepMould, we specialize in providing unparalleled injection mold manufacturing services tailored to our clients' diverse needs. Our commitment to quality and innovation has positioned us as a top choice among industry leaders.
Our capabilities encompass:
- Comprehensive Design Assistance: From prototyping to full-scale production, our team collaborates closely to ensure the best outcomes.
- Advanced Machining Processes: Techniques that guarantee precision machining on all parts.
- Rigorous Testing and Quality Assurance: Every product undergoes stringent quality testing before delivery.
Why Choose DeepMould?
Here are several reasons why partnering with DeepMould will elevate your production capabilities:
- Expert Knowledge: Our team is composed of experienced professionals with a wealth of knowledge in injection molding and metal fabrication.
- Customer-Centric Approach: We pride ourselves on excellent customer service and support, ensuring each project aligns with client expectations.
- Timely Delivery: We understand the importance of timelines and strive to deliver all projects promptly.
Future Trends in Injection Molding
The future for the injection mold manufacturer looks bright, with several trends expected to shape the industry:
1. Increased Sustainability
As environmental concerns rise, there is a concerted effort to develop and implement sustainable practices, such as:
- Developing biodegradable materials to reduce landfill waste.
- Implementing recycling processes for leftover materials from manufacturing.
- Emphasizing energy-efficient operations across the board.
2. Customization and Personalization
The increasing demand for personalized products is leading to:
- More flexible manufacturing systems that can adapt to individual client needs.
- Advanced software for modeling and visualizing customized pieces before production.
3. Enhanced Collaboration and Global Sourcing
With the world becoming more interconnected, manufacturers are leveraging global resources for more efficient production:
- Collaborative designs with partners worldwide to reduce lead times.
- Integrating international supply chains to source the best materials and components.
Conclusion
The role of an injection mold manufacturer is fundamental in the landscape of metal fabrication. As technology advances and market demands evolve, manufacturers are called to adapt and innovate continually. Choosing a dedicated and professional partner like DeepMould guarantees high-quality products that meet the industry's rigorous standards. With an emphasis on precision, sustainability, and customer-centric solutions, we are committed to leading the charge in the future of injection molding.
For more information about our services or to discuss your specific requirements, please visit us at DeepMould.net. We look forward to collaborating with you!