A Comprehensive Guide to Teflon Tubing Fittings
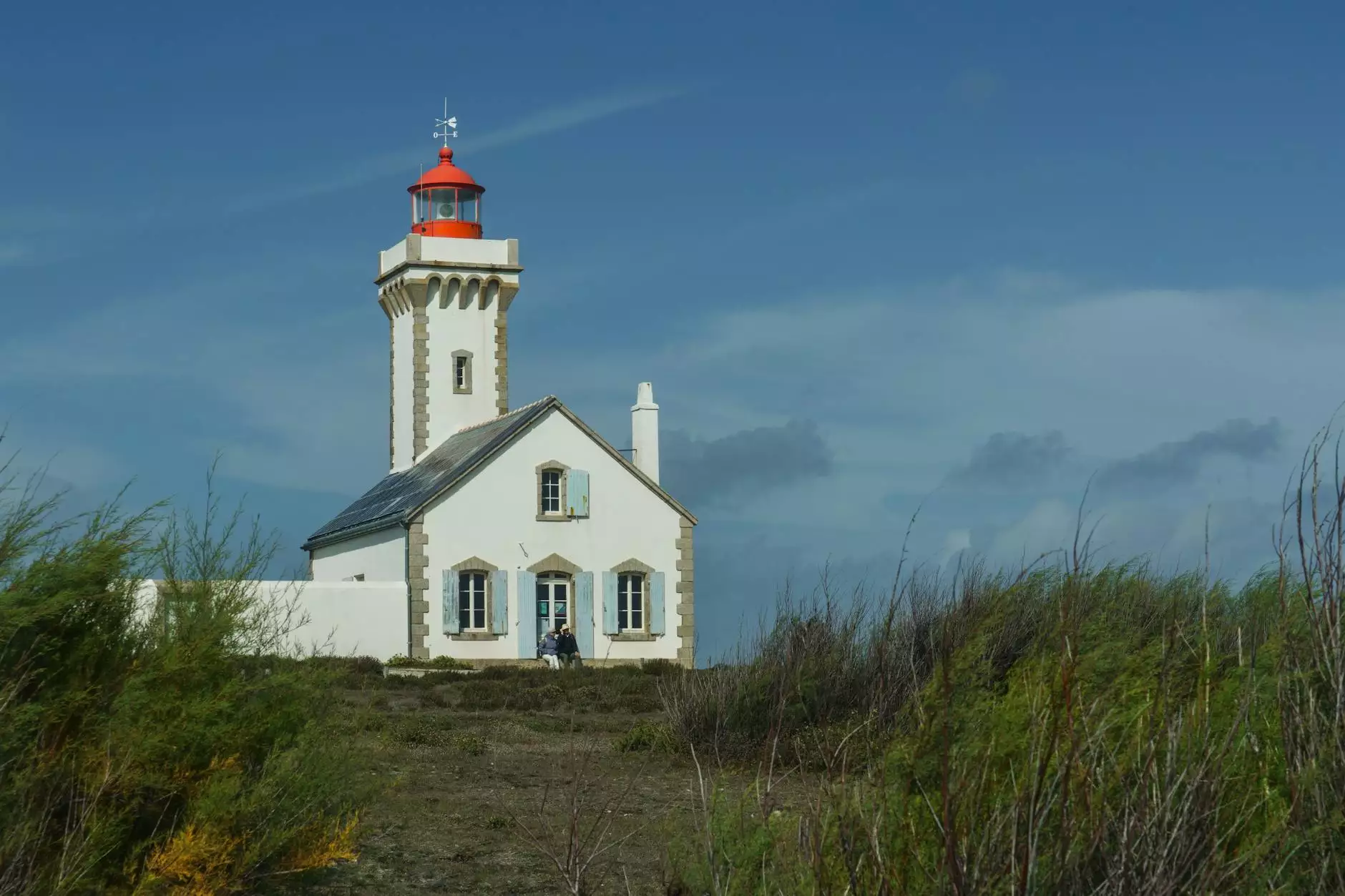
Teflon tubing fittings have become essential components in various industrial applications due to their superior chemical resistance and temperature capabilities. This article explores everything you need to know about Teflon tubing fittings, including their characteristics, the advantages they offer, and practical applications across different industries.
What are Teflon Tubing Fittings?
Teflon tubing fittings are specialized connectors made from polytetrafluoroethylene (PTFE), commonly known as Teflon. These fittings are designed to connect Teflon tubing to other pipes, valves, or equipment, ensuring a secure and leak-proof connection. Due to their excellent performance in harsh environments, they are widely used in chemical processing, pharmaceuticals, food and beverage, and various other fields.
Key Features of Teflon Tubing Fittings
When considering teflon tubing fittings, it’s essential to understand their key features that significantly contribute to their widespread use:
- Chemical Resistance: Teflon is highly resistant to acids, bases, and solvents, making these fittings ideal for transporting hazardous and corrosive materials.
- Temperature Tolerance: Teflon tubing fittings can withstand extreme temperatures, ranging from -200°C to +260°C, offering versatility in various applications.
- Low Friction Coefficient: The low friction properties of Teflon make it easier for fluids to flow through the tubing, enhancing efficiency in processes.
- Non-stick Surface: Teflon’s non-stick characteristics minimize clogging and buildup, which is crucial in maintaining clean and efficient operations.
- Durability: These fittings are resistant to wear and tear, ensuring a long lifespan even under demanding conditions.
Advantages of Using Teflon Tubing Fittings
Beyond their physical properties, teflon tubing fittings confer numerous advantages that enhance operational efficiency:
- Improved Safety: By preventing chemical leaks and reactions, Teflon fittings contribute to a safer working environment for employees and facilities.
- Cost-efficiency: The long lifespan and reduced maintenance requirements of Teflon fittings can lead to lower operational costs over time.
- Versatility: With applications across multiple industries, Teflon fittings prove to be versatile solutions in fluid transfer systems.
Applications of Teflon Tubing Fittings
Teflon tubing fittings can be found in various sectors, each utilizing these advanced components to optimize their operations:
Chemical Industry
In the chemical industry, Teflon fittings are crucial for handling aggressive chemicals. Their durability and chemical resistance make them perfect for use in reactant transfer, storage tanks, and mixing applications.
Pharmaceutical Sector
For pharmaceutical manufacturing, cleanliness and safety are paramount. Teflon tubing fittings meet stringent hygiene standards, making them suitable for applications involving drugs and medical devices.
Food and Beverage Production
With increasing regulations in food safety, Teflon fittings are ideal for applications in food processing and beverage production due to their non-stick surface and ease of cleaning.
Pneumatic Systems
In pneumatic applications, Teflon fittings help maintain air quality and prevent contamination, ensuring efficient operation and reliability in automated systems.
Choosing the Right Teflon Tubing Fittings
Selecting the appropriate Teflon tubing fittings for your application involves considering several factors:
- Compatibility: Ensure that the fitting material is suitable for the fluids being transported. Teflon should be compatible with the chemicals in use.
- Size: Proper sizing of fittings is critical for optimal flow and to prevent leaks.
- Connection Type: Determine the type of connection required, whether it be threaded, smooth, or quick connect, to ensure a secure fit.
- Pressure Ratings: Check the pressure rating of the fittings to ensure they can handle the system's requirements.
Installation Tips for Teflon Tubing Fittings
Proper installation is key to leveraging the advantages of Teflon tubing fittings effectively. Here are some best practices:
- Clean Surfaces: Ensure that the surfaces of both the Teflon tubing and fittings are clean and free from contaminants before assembly.
- Use the Right Tools: Utilize suitable tools to avoid damaging the fittings during installation. Torque wrenches can help achieve the right tightness.
- Test for Leaks: After installation, conduct a test for leaks by running the system at low pressure. Gradually increase to the intended levels.
- Periodic Inspection: Regularly inspect the fittings for wear and signs of failure to maintain system integrity.
Maintenance of Teflon Tubing Fittings
To ensure longevity and optimal performance, routine maintenance of Teflon tubing fittings is essential:
- Visual Inspections: Regularly check fittings for signs of leakage, cracks, or damage.
- Cleaning: Depending on the application, clean the fittings periodically to remove any buildup that may cause blockages.
- Functionality Checks: Perform tests to ensure that flow rates and pressures remain within specifications.
Conclusion: The Future of Teflon Tubing Fittings in Industrial Applications
As industries continue to seek advanced materials that provide safety, efficiency, and durability, teflon tubing fittings will remain at the forefront of manufacturing and processing solutions. Their unique properties cater to the demands of a variety of sectors, making them indispensable components in modern industrial applications.
Choosing high-quality Teflon tubing fittings from reputable valve suppliers and fittings manufacturers like Samvay Global ensures that your operations maintain optimal performance while adhering to safety and compliance standards. As innovations in materials science evolve, the applications for Teflon fittings are set to expand even further, solidifying their role in the future of industrial solutions.