Understanding H2S Monitor Calibration: Ensuring Safety and Compliance
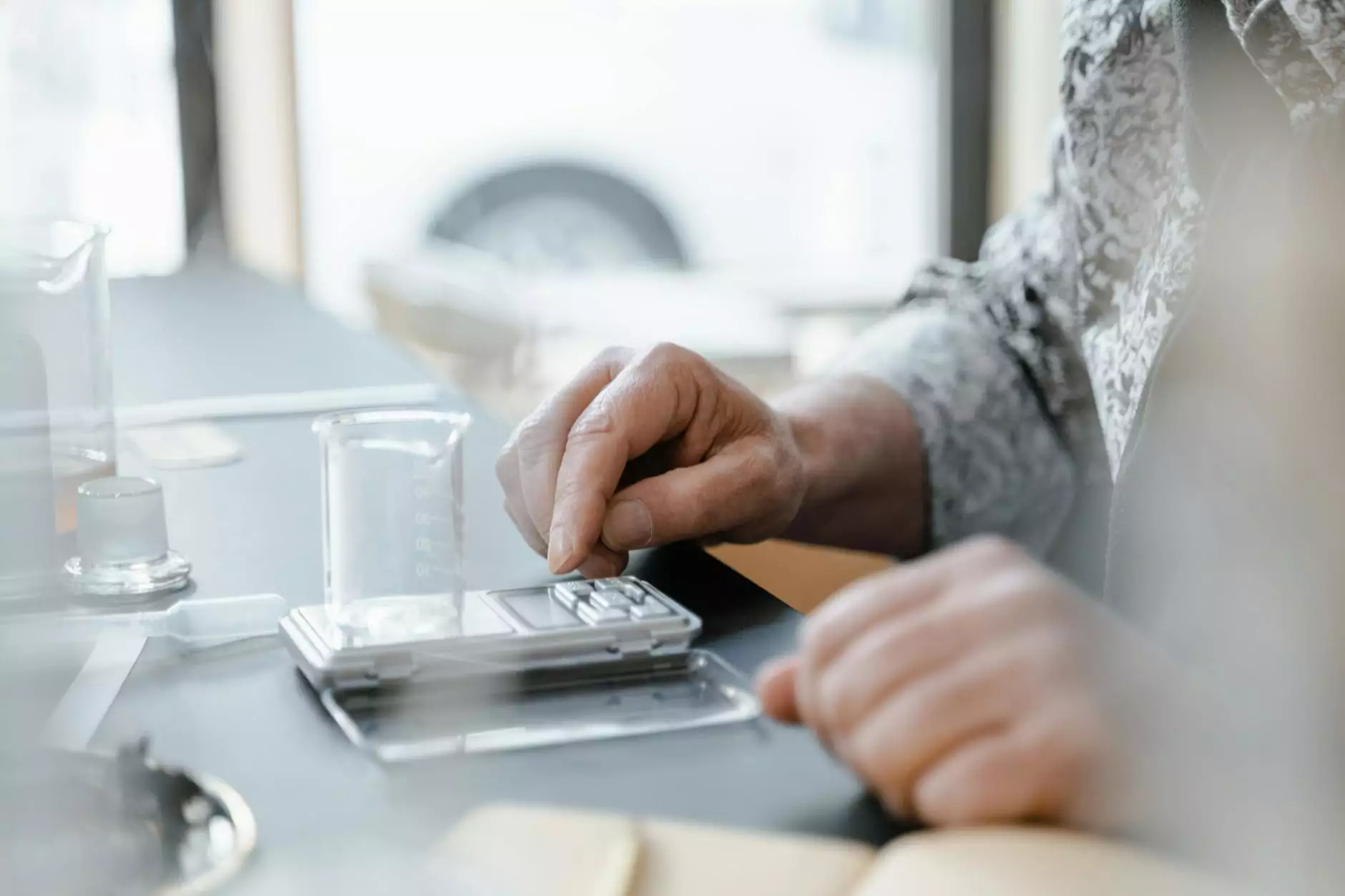
Hydrogen sulfide (H2S) is a toxic gas commonly found in various industrial and environmental settings. Effective monitoring of this gas is critical for the safety of workers, especially in industries such as oil and gas, wastewater treatment, and mining. One of the most crucial aspects of maintaining safety in these environments is H2S monitor calibration. This article delves into the significance of accurate calibration, methods to ensure correct measurements, and the overall impact on workplace safety.
The Importance of H2S Monitor Calibration
Calibration of H2S monitors is essential for several reasons:
- Accuracy: Calibration ensures that the monitor provides accurate readings of H2S levels, reducing the risk of false alarms or failure to detect dangerous concentrations.
- Compliance: Many regulatory bodies require periodic calibration of gas monitors to comply with safety standards.
- Worker Safety: An improperly calibrated monitor can lead to life-threatening situations for workers exposed to hazardous environments.
- Equipment Longevity: Regular calibration can increase the lifespan of monitoring equipment by ensuring that it is functioning correctly and maintained.
Understanding the H2S Monitor Calibration Process
The calibration process involves comparing the readings from the H2S monitor with known concentrations of hydrogen sulfide. Below are the general steps involved:
1. Gathering Calibration Standards
Before calibration, it is essential to obtain calibration gases of known concentrations. This ensures that the monitors are being tested against accurate benchmarks.
2. Connecting the Monitor
Connect the H2S monitor to the calibration system, ensuring that all connections are secure and free from leaks. This will prevent any inaccuracies during the calibration process.
3. Adjusting the Monitor
Once the monitor is connected, it may require adjustment to align its readings with the calibration standards. This step is crucial for ensuring that the monitor provides correct readings in a real-world scenario.
4. Testing the Calibration
After adjustments, the monitor should be exposed to the calibration gas for a specified duration. This step confirms that the monitor responds accurately to changes in H2S concentration.
5. Documenting the Results
It is vital to document the calibration results, including initial readings, adjustments made, and final outcomes. This documentation serves as proof of compliance and as a reference for future calibrations.
Best Practices for H2S Monitor Calibration
To ensure effective H2S monitor calibration, consider the following best practices:
1. Regular Calibration Schedule
Establish a regular calibration schedule based on the manufacturer's recommendations and the environment in which the monitor operates. For instance, more aggressive environments may require more frequent calibration.
2. Training and Competency
Ensure that staff involved in calibration are trained thoroughly. Proper training increases the chances of accurate calibration and enhances workplace safety.
3. Use Quality Calibration Equipment
Invest in high-quality calibration equipment. The precision of the calibration gases and the calibration device significantly influences the outcome of the calibration process.
4. Track Calibration Data
Maintain a log of calibration data, including dates of calibration, results, and any maintenance conducted on the monitor. This log will help identify patterns or issues that may arise over time.
5. Calibration in Real-time Conditions
Where possible, conduct calibrations in conditions that closely mimic real-world environments. This approach ensures that the monitor performs accurately under actual operating conditions.
Impact of Accurate Calibration on Business Operations
Accurate calibration of H2S monitors directly influences business operations in various ways:
1. Enhancing Employee Morale and Safety
When employees feel that their safety is prioritized through accurate monitoring, it enhances morale and productivity. A safe working environment fosters loyalty and minimizes turnover rates.
2. Reducing Liability Risks
Companies that ensure proper H2S monitor calibration reduce their liability risks. With proper documentation and accurate monitoring, they are better protected against potential lawsuits arising from workplace incidents.
3. Regulatory Compliance
Compliance with health and safety regulations is vital for any business. Regular calibration helps maintain compliance with regulations set by OSHA and other governing bodies, thereby avoiding costly fines and legal issues.
4. Minimizing Operational Downtime
Through effective calibration, businesses can minimize operational downtime caused by sensor failures. Monitors that are functioning optimally contribute to a smooth operational flow, enhancing overall productivity.
Conclusion
In conclusion, H2S monitor calibration is an indispensable part of maintaining safety and compliance in industries where hydrogen sulfide exposure is a risk. Ensuring accuracy through regular calibration not only protects workers but also enhances overall business operations. By following best practices, investing in quality equipment, and committing to thorough training, companies can significantly mitigate the dangers posed by H2S and contribute to a safer workplace.
For more information on effective H2S monitor calibration techniques and to explore educational services related to safety and compliance training, visit h2sonlinetraining.com.