Understanding the Role of a Plastic Injection Molding Manufacturer
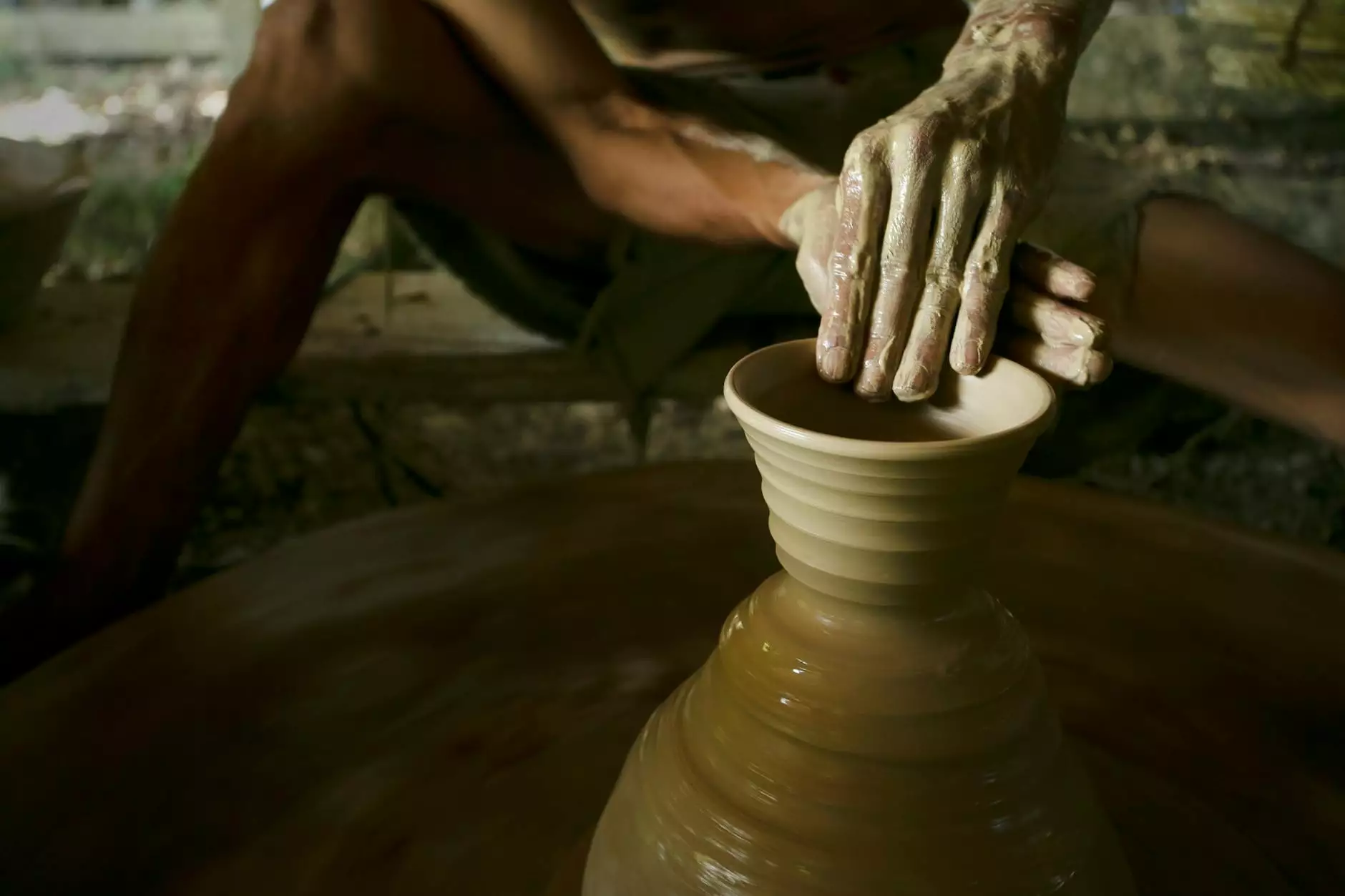
Plastic injection molding is an innovative manufacturing process that shapes plastic into a variety of forms, serving countless industries. As a prominent plastic injection molding manufacturer, DeepMould is dedicated to providing exceptional quality, efficiency, and creativity in all our projects. This article delves into the intricacies of plastic injection molding, the benefits it offers, and why we stand out as a leader in the industry.
What is Plastic Injection Molding?
Plastic injection molding is a manufacturing process where melted plastic is injected into a mold cavity, resulting in a solid and often complex finished product. This method is celebrated for its efficiency and high level of precision, making it ideal for creating intricate shapes and designs. The process typically involves several key steps:
- Material Selection: Choosing the right type of plastic is crucial depending on the end-use requirements.
- Melt Process: The selected plastic resin is heated until it melts into a viscous liquid.
- Injection: The molten plastic is injected into a mold under high pressure.
- Cooling: The injected plastic is allowed to cool, solidifying in the shape of the mold.
- Finishing: Once cooled, the mold is opened, and the finished parts are ejected.
Why Choose Plastic Injection Molding?
As industries evolve, the demand for precision engineering solutions grows. Plastic injection molding offers numerous advantages that make it a preferred choice in manufacturing:
1. High Efficiency and Speed
The injection molding process is remarkably quick. Once the mold is created, producing parts takes mere seconds to minutes, significantly reducing production time and costs.
2. Consistency and Reproducibility
Once a mold is designed, it can produce thousands of identical parts with minimal variation. This consistency ensures quality and reliability, crucial factors for manufacturers and consumers alike.
3. Cost Effectiveness
Although the initial cost of tooling is significant, the per-unit cost decreases as production volume increases, making it a highly economical choice for mass production.
4. Design Flexibility
Modern techniques allow for precise and intricate designs, enabling manufacturers to push the boundaries of what is possible with plastic components.
DeepMould: Your Trusted Plastic Injection Molding Manufacturer
At DeepMould, we pride ourselves on being a leading plastic injection molding manufacturer. Our extensive experience in the industry has equipped us with the knowledge and skills necessary to excel in this competitive field. Here's what sets us apart:
Commitment to Quality
Quality assurance is at the heart of everything we do. From selecting the highest-grade materials to employing advanced quality control measures, we ensure that every product meets or exceeds industry standards.
Advanced Technology and Equipment
We invest in cutting-edge technology and advanced machinery that enhance our manufacturing capabilities. This commitment allows us to offer high precision and maintain efficiency in production.
Expert Team of Professionals
Our team consists of highly skilled professionals who are dedicated to delivering exceptional service. From design to implementation, our experts work closely with clients to ensure their vision is realized.
The Applications of Plastic Injection Molding
Plastic injection molding finds its applications across a wide range of industries:
1. Automotive Industry
In the automotive sector, the use of durable and lightweight plastic components significantly enhances vehicle performance and fuel efficiency. Parts such as dashboards, connectors, and body panels are often produced using injection molding.
2. Consumer Goods
Everyday items such as containers, toys, and appliances utilize plastic injection molding. The ability to create customized parts allows for innovation and variety in product offerings.
3. Medical Devices
In the medical field, precision is paramount. Plastic injection molding facilitates the manufacture of intricate medical devices and components, ensuring safety and reliability.
4. Electronics
Electronic devices often require high precision components. Cases, connectors, and insulators are frequently produced through this efficient manufacturing process.
Eco-Friendly Practices in Plastic Injection Molding
The growing emphasis on sustainability has led to the adoption of eco-friendly practices within the plastic injection molding industry. At DeepMould, we are committed to minimizing our environmental footprint by:
1. Utilizing Recyclable Materials
We prioritize the use of recyclable plastics whenever possible, aligning with global efforts to reduce waste and promote recycling.
2. Implementing Energy-Efficient Processes
By optimizing machine use and reducing energy consumption, we aim to lessen our impact on the environment while maintaining productivity.
Conclusion: The Future of Plastic Injection Molding
The plastic injection molding industry is poised for continuous growth and innovation. Advancements in technology, coupled with increasing demands for customized solutions, indicate a promising future. DeepMould remains committed to leading the charge in this dynamic landscape, empowering businesses with top-tier manufacturing solutions.
As a premier plastic injection molding manufacturer, we are ready to collaborate with you to bring your ideas to life. Our focus on quality, efficiency, and sustainability ensures that we not only meet your needs but also advance your business objectives. Contact us today at DeepMould.net to learn more about how we can support your plastic injection molding requirements!